Als einer der ersten Hersteller hat Volvo schon 2017 den Abschied vom Verbrenner-Motor eingeleitet. Als erstes wurde die Entwicklung neuer Dieselmotoren gestoppt, seit 2019 sollen alle neuen Modelle – aber nur ganz neue, keine Facelifts – immer elektrifiziert vorfahren: also mit stromunterstützten Mild-Hybrid-Antrieben, als Plug-in-Modell mit Steckdosen-Anschluss oder als reines Elektroauto. Von letzteren wollen die Schweden künftig jedes Jahr eines auf den Markt bringen, ab 2025 soll jeder zweite verkaufte Volvo ein Batterie-Auto sein, reine Verbrenner ab dann der Geschichte angehören.
Das sind große Pläne für einen Hersteller, der Stand heute nicht gerade mit sparsamen Motoren glänzt und keinen einzigen Stromer im Programm hat. Der kommt erst Ende 2020, in Form des XC40 Recharge, einem Kompakt-SUV mit voraussichtlich rund 400 Kilometern Reichweite. Zugegeben: Ganz unbedarft ist Volvo auf dem Strom-Terrain nicht. Immerhin hat die Marke selbst schon einige Hybride im Angebot und einst mit der Kleinserie "C30 electric" Erfahrungen gesammelt. Außerdem haben die Schweden mit Polestar seine eigene E-Marke gegründet und der chinesische Mutterkonzern Geely sowie Volvos Lifestyle-Schwester Lynk & Co sind auf dem Heimatmarkt schon länger mit Batterie-Modellen unterwegs.
Die Technik für den Elektro-XC40 ist kein Hexenwerk, das City-SUV nutzt die kompakte Konzern-Plattform CMA, auf der neben dem Polestar 2 auch der Geely F11 und alle Lynk-&-Co-Modelle aufbauen. Am spannendsten ist, im wahrsten Sinne des Wortes, wie bei jedem Elektro-Auto der Akku. Den fertigt Volvo ab sofort selbst: Im Werk im belgischen Gent, wo der XC40 vom Band läuft, hat der Autobauer seine erste Batterie-Fertigung in Betrieb genommen; die nächste soll am neuen US-Standort in Charleston/South Carolina folgen.
Zellen stammen weiterhin von Zulieferern
Allerdings: Volvo übernimmt in seinen Werken nur die Montage der Batterie-Pakete fürs Auto. Die Zellen, also die eigentlichen Stromspeicher, beziehen die Schweden weiterhin von Zulieferern, konkret von CATL aus China und dem südkoreanischen Lieferanten LG Chem. Daran soll sich so schnell auch nichts ändern, so Geert Bruyneel, bei Volvo verantwortlich für die Produktion: "Aktuell haben wir keine Pläne, unsere eigene Zellproduktion zu starten."
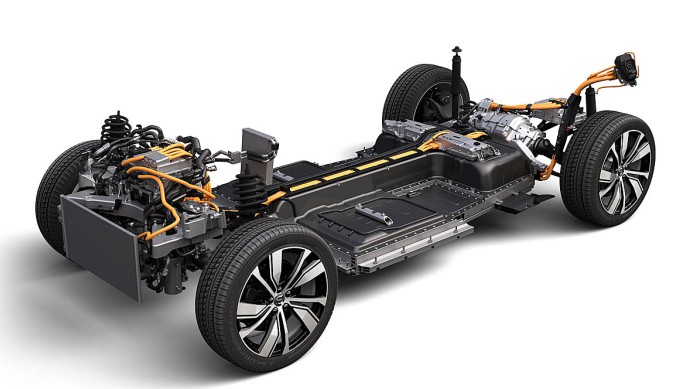
Anders sieht es bei der Konkurrenz aus: VW plant, zusammen mit Northvolt eine Zellfertigung aufzunehmen, die Opel-Mutter PSA verfolgt das gleiche Ziel zusammen mit der Total-Tochter Saft und auch Tesla will künftig unter anderem in Brandenburg seine eigenen Zellen herstellen. Das ist logisch, macht doch der Akku derzeit rund 40 Prozent des Wertes eines Elektroautos aus. Nur ein Prozent der weltweiten Batterieproduktion kommt aber aus Europa, die hiesige Autoindustrie ist aktuell also von Zulieferern abhängig, was fatale Folgen haben kann. Die aktuelle Corona-Krise macht deutlich sichtbar, wie schnell internationale Lieferketten ins Stocken geraten können. Der Transport der schweren Zellen rund um den Globus ist zu dem nicht nur teuer, sondern auch CO2-intensiv. Das hat allerdings auch die asiatische Konkurrenz erkannt und drängt nach Europa: CATL beispielsweise arbeitet an einem Werk in der Nähe von Erfurt, wo künftig Batteriezellen mit einem Energiegehalt von 100 Gigawattstunden jährlich produziert werden sollen – das reicht für gut eineinhalb Millionen E-Autos.
Es geht auch um Prestige und Arbeitplätze
Dass es für die europäischen Autobauer bei der Zellproduktion dabei auch um Prestige und Arbeitsplätze ist klar: Die hiesige Expertise in der Entwicklung und dem Bau von Verbrennungsmotoren verliert an Bedeutung, und mehr und mehr Produktionsbänder für Einspritzanlagen und Tanks, Kolben, Pleuel und Nockenwellen, Auspuffanlagen und Katalysatoren dürften in naher Zukunft stillstehen. Doch wer am Ende das Rennen in Sachen Akku-Fertigung macht, ist noch offen.
Volvo jedenfalls ist sich sicher, dass schon die eigene Batteriemontage direkt am Werk ein großer Vorteil ist. Eine Fertigung vor Ort, so Bruyneel, seit mit Blick auf Lieferzeiten und Transportkosten auf jeden Fall effizienter. Und außerdem will man die Dinge wohl auch gerne weit möglichst in der Hand behalten. "Wenn wir die Batterien selbst zusammenbauen", so der Manager, "haben wir letztlich auch eine bessere Kontrolle über die Qualität und das gesamte Produkt."