Kurzfassung
Im polnischen Gliwice hat Tenneco ein Technologiezentrum eröffnet, um die Fahrwerke der Zukunft zu entwickeln. Wir waren bei der feierlichen Eröffnung vor Ort und durften einen Blick hinter die Kulissen werfen.
Der Boom der Elektroautos macht neue Fahrwerkstechnologien notwendig: Schließlich erreichen die Fahrzeuge Gewichte von fast drei Tonnen und haben dabei Beschleunigungswerte eines Sportwagens. Auch das autonome Fahren wirft seine Schatten voraus: In Zukunft soll der Fahrzeuginnenraum immer mehr zum Arbeitsplatz oder Freizeitraum umfunktioniert werden. Hier stören dann Unebenheiten des Bodens gewaltig. Die Passagiere sollen sich wie in einer Sänfte fühlen, folglich muss die Dämpfung alle Unebenheiten ausfiltern.Modernste Büros
Um die Fahrwerke der Zukunft bauen zu können, hat der amerikanische Hersteller Tenneco Ende Mai im polnischen Gliwice ein neues Technologiezentrum eröffnet. asp AUTO SERVICE PRAXIS war live vor Ort. In dem Technologiezentrum mit 9.600 Quadratmetern Fläche arbeiten zukünftig 240 Ingenieure. Im angeschlossenen Prototypenzentrum können die Entwicklungen dann auch hergestellt und in Zusammenarbeit mit den Fahrzeugherstellern gestestet werden. Zu den Hauptprodukten, die in dem neuen Center entwickelt und getestet werden, zählen passive Dämpfer und Module von Monroe OE Solutions sowie semiaktive Gewindedämpfer und Module von Monroe Intelligent Suspension. Diese Technologien kommen in Millionen von neueren Pkw, Nutzfahrzeugen, Bussen und Lkw zum Einsatz.
Der Standort ist außerdem für die Konstruktion zahlreicher Kernbauteile verantwortlich, die in den Dämpfern von Monroe OE Solutions und Monroe Intelligent Suspension verbaut werden, einschließlich Ventilsystemen, Führungs- und Dichtsystemen sowie Strukturbauteilen und -materialien. Darüber hinaus betreut das neue Center die Testfahrtaktivitäten in Europa, bei denen Ingenieure von Tenneco gemeinsam mit den Fahrzeugherstellern die Dämpferventiltechnik vor der Markteinführung eines neuen Fahrzeugmodells testen und finalisieren.
"Mit diesem beeindruckenden neuen Standort können unsere Mitarbeiter der Abteilungen Ride Control und Advanced Suspension Technologies die Einführung unserer Technologien beschleunigen und deren Wert für globale OEMs steigern", erklärt Romain Nollet, Group Vice President und General Manager von Ride Control bei Tenneco.
Laut Tenneco gehört das Werk zu den modernsten in Europa, auch was die Gestaltung der Arbeitsräume und die technische Ausstattung betrifft. So sind beispielsweise die Büroräume, wo Entwickler an ersten Fahrwerks-Innovationen am Computer arbeiten, offen und modern gestaltet und durch spezielle schallschluckende Materialien so leise, dass sich die Mitarbeiter voll und ganz auf ihre Arbeit konzentrieren können. Dank modernster Programme und IT-Systeme können ganze Fahrwerkssysteme schon am Rechner entworfen werden.
Tenneco Gliwice Eröffnung
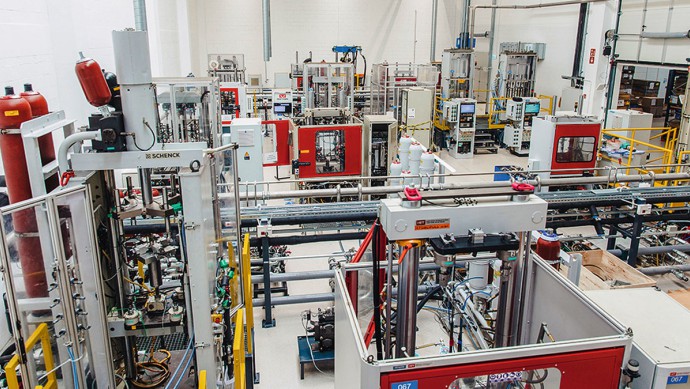
- Ausgabe 6/2023 Seite 024 (1.1 MB, PDF)
Sand aus fernen Ländern
Ist die Designphase geschafft, können in der 5.330 Quadratmeter großen Werkstatt des Standorts Prototypen aller Arten von passiven und semiaktiven Dämpfern hergestellt und geprüft werden. Vor Ort sind Festigkeits-, Haltbarkeits-, Korrosions-, Leistungs- und Geräuschprüfungen sowie Computer-Simulationen der Bauteil- und Produktleistung möglich. So lassen sich auf den Maschinen beispielsweise sämtliche Belastungszustände eines Stoßdämpfers simulieren, denen er im echten Einsatz ausgesetzt ist. Darunter Schütteln, Einfedern oder Vibrationen, die auftreten. Auch auf Korrosion wird der Dämpfer getestet, und das sogar länderspezifisch: Es stehen verschiedene Sorten Sand aus verschiedensten Ländern zur Verfügung, um die Auswirkungen auf das Dämpferleben perfekt simulieren zu können. Denn die Dämpfer müssen nach den Vorgaben der Autohersteller in den meisten Fällen mindestens 150.000 Kilometer oder zehn Jahre Einsatz überstehen können.
Ist diese Phase geschafft, gehen die Tests am Auto weiter: Ein Dämpfer lässt sich so modifzieren, bis er schließlich perfekt zum Fahrzeug und zum vermittelten Fahrgefühl passt. Das kann sogar innerhalb einer Fahrzeugreihe variieren, je nachdem, ob das Auto eher sportlich oder auf Bequemlichkeit abgestimmt sein soll. Die Entwicklung von Fahrwerken nimmt je nach Projekt mehrere Jahre in Anspruch, bis sie schließlich in die Serienfertigung gehen.